Engineering Chain for Tackling Big Jobs
For moving heavy equipment and handling shock loads, choose engineering class drive chains. Built for tough conditions, engineering chains offer high load capacity and fatigue strength for long-lasting performance.
There are two main types: drive chains and conveyor chains, both used for power transmission. Drive chains withstand harsh environments like mud, sand, and metal fines.
Engineering-class Chain configurations
The engineering class drive chain is comprised of a series of links assembled by inserting pins and bushings between pairs of metal plates known as sidebars. These interconnected links create a continuous chain that facilitates power transmission, typically from a small driving sprocket to a larger driven one on parallel shafts.
The two primary chain types are straight and offset sidebar chains. Other engineering chain types with limited application in drive systems include steel-bushed rollerless chains and welded steel mill chains. Steel-bushed chain is primarily utilized for bucket elevators, while welded steel chain, a variation of offset chain, features bushings welded between the sidebars instead of press-fitted and is commonly used in wood, pulp, and paper applications.
Straight sidebar chain
A straight sidebar chain comprises alternating connections of pin links and bushing links. Each bushing link features a pair of sidebars connected by two press-fit bushings, while each pin link is connected by two press-fit pins. The pin and bushing links are arranged alternately, with the pin from one link fitting inside the bushing of the adjacent link, enabling each link to flex in a single plane.
Straight sidebar chains are suitable for accepting attachments and are predominantly employed in conveyor applications. However, certain drive applications necessitate the use of a straight sidebar chain due to factors such as a short pitch (distance between pin holes in sidebars) or thick sidebars that cannot accommodate an offset. In such scenarios, straight sidebar chains are utilized for drive applications.
Offset sidebar chain
Offset sidebar chains are typically favored for high-load applications due to their ease of length adjustment. Unlike a straight sidebar chain, every link of the offset chain is identical, featuring one pin and one bushing connecting a pair of bent sidebars, as illustrated in Figure 2. The pin of one link fits inside the bushing of the next link, with pins press-fitted into the sidebars and secured in place with cotter pins.
Most chain drives can be adjusted to spread the shafts farther apart to compensate for chain elongation. However, eventually, shortening the chain may be necessary. As all links of an offset chain are identical, a single link can be removed to shorten the chain and compensate for elongation caused by pin-and-bushing wear. In contrast, links of straight sidebar chains must be removed in pairs.
The wear of pin and bushings in an offset chain is influenced by how the chain articulates around a sprocket, which, in turn, is determined by the orientation of the link. Wear is typically reduced when the narrow end of the link faces the smaller sprocket. Consequently, the offset chain tends to experience slower elongation compared to a straight sidebar chain.
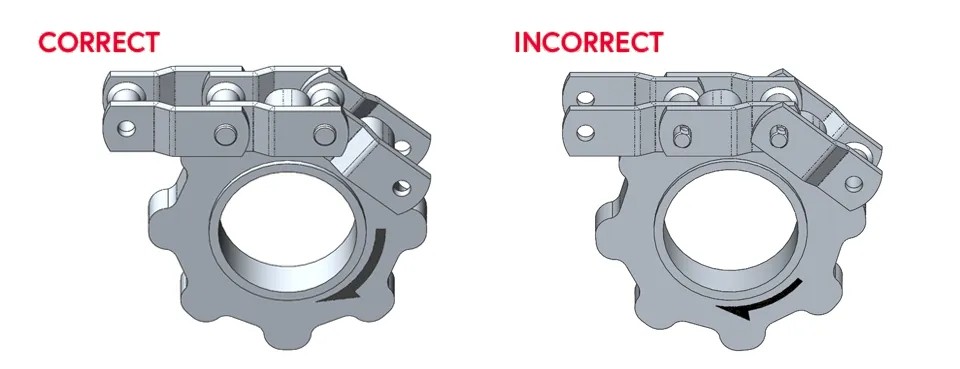
Many drive chains feature hardened (42 Rockwell C) steel rollers placed over the bushings. These rollers engage with the sprocket teeth, acting as bearings to minimize friction and wear. Engineering class chains equipped with rollers share similarities with conventional roller chains in design but differ in size, strength, tolerances, and ability to operate under adverse conditions. Engineering class chains generally support higher loads but operate at lower speeds.
CTS®-ChinaTransmissionS is a professional agricultural chain manufacturer in the power transmission industry. As an experienced agricultural chain supplier, we manufacture Welded Steel Mill Chains with high-quality steel material. Besides standard agricultural chains, we can also provide customized agricultural chains for your application.
We offer a wide range of industrial transmission chain options: drop forged rivet-less chains, welded steel chains, 81X lumber conveyor chains, roller chains, conveyor chains, heavy-duty roller chains, etc.
If you have any questions about industrial transmission chains, please contact us to help you.