Agricultural Machinery

- Heat treatment
- Precision Machining
- Assembly process
- QC
- Crafts improvement
Ability
Heat Treatment
Key steps in the heat treatment process of CTS
When it comes to CTS's advanced heat treatment process, CTS focuses on significantly improving the hardness and wear resistance of the sprocket chain through precise control of temperature and quenching processes. CTS’s heat treatment process uses the following key steps to infuse superior performance into the sprocket chain: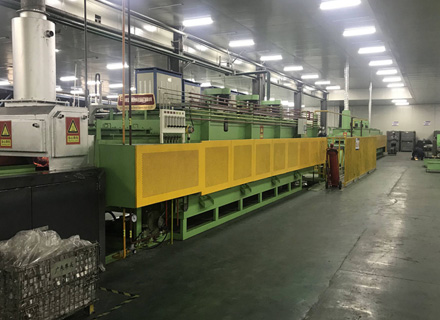
Precise temperature control
We use advanced heat treatment equipment capable of controlling within a very narrow temperature range. This ensures that the sprocket chain reaches the exact critical temperature during the heating phase, laying a solid foundation for the subsequent quenching and tempering steps.
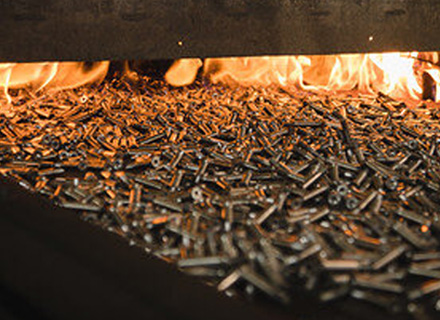
Quenching process optimization
We carefully design and optimize the quenching process to ensure that both the surface and internal crystal structure of the sprocket chain can undergo uniform and dense changes under rapid cooling. This helps increase overall stiffness, allowing the product to maintain excellent performance under high loads and harsh environments.
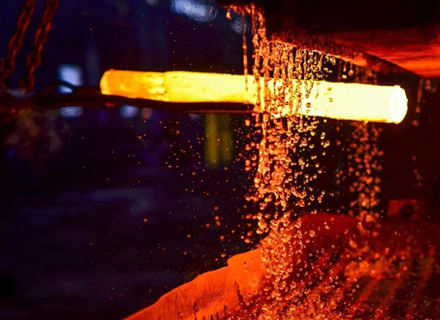
Tempering control
After quenching, we perform precise tempering, controlling temperature and time to achieve the ideal balance of hardness and toughness. This not only helps to reduce the brittleness of the sprocket chain, but also increases its wear resistance under severe friction and high load conditions.
CTS heat treatment process case
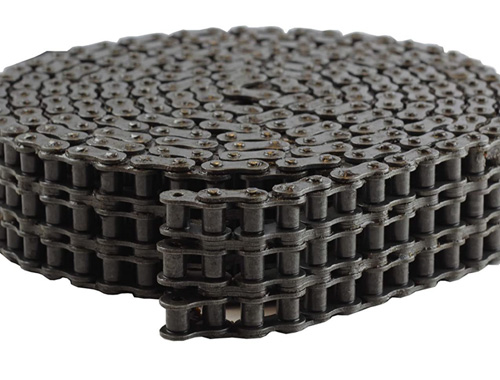
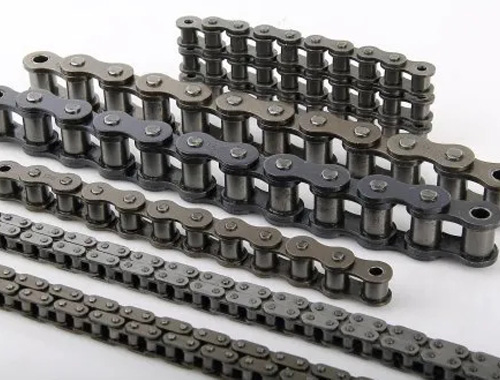
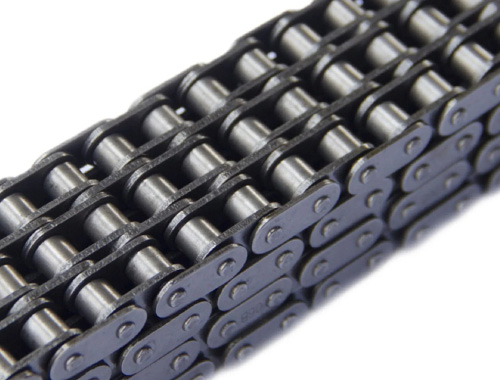

Contact us now to inquire about your heat treatment customization needs
Contact nowAbility
Precision Machining
The precision machining process we are proud of is the core to ensure the excellent performance of the sprocket chain, through the use of state-of-the-art highly automated equipment and continuous technological innovation.
Highly automated manufacturing
Turning
Turning is a manufacturing process that involves rotating a workpiece and cutting material with a tool. In the manufacture of industrial sprockets and gears, the turning process plays a vital role in the accuracy of the shape and the smoothness of the surface.
High precision:Turning can be used to precisely cut the shape of industrial sprockets and gears to ensure that their geometry meets design requirements. This is critical to drivetrain stability and efficiency.
Ensure surface flatness: The turning process can provide a surface with higher flatness, which helps to reduce the friction and wear of industrial sprockets and gears during movement.
Through advanced turning equipment and technology, we are able to achieve micron-level precision, ensuring that the shape and surface flatness of each industrial sprocket and gear meet the highest standards. This precise turning process is the basis for high-quality sprocket chains.
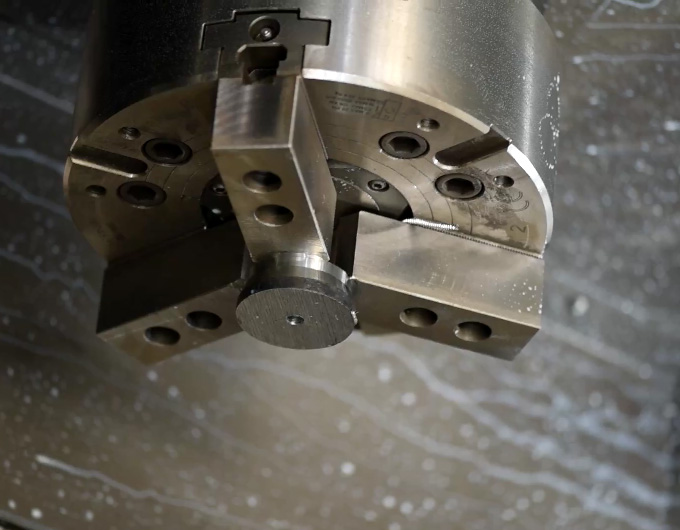
Milling
Milling is a manufacturing process in which a tool is moved over a workpiece to remove material to form the desired shape. In the production of sprocket chains, the milling process is used to create specific contours and grooves.
Precise formation of contours and grooves:Milling allows us to form the various contours and grooves on the sprocket chain according to the design requirements, ensuring that it will fit accurately with other components.
Surface finish: Milling can provide a relatively smooth surface, which helps reduce friction in the movement of the sprocket chain and prolongs its service life.
CTS uses high-precision milling equipment and advanced tool technology to ensure that every contour and groove of the sprocket chain meets the design requirements. This precision milling process is integral to achieving a high-quality sprocket chain.
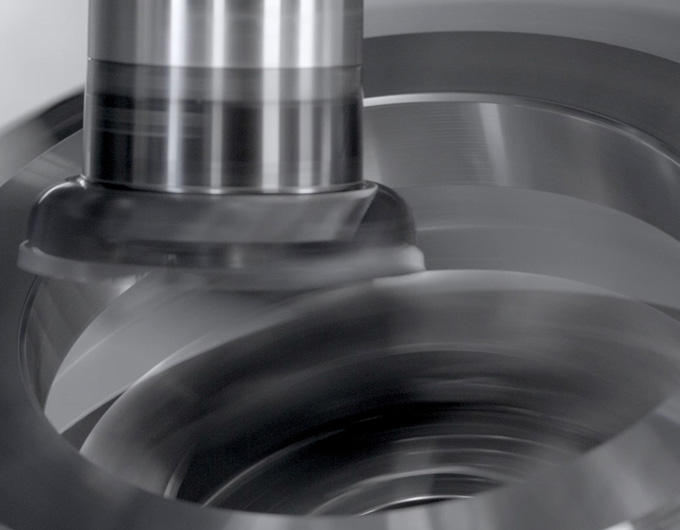
Grinding
Grinding is a machining process that uses abrasive particles to cut a workpiece to form a precise shape. In the manufacture of sprocket chains, grinding processes are often used to improve dimensional accuracy and surface smoothness.
Dimensional accuracy:Grinding enables extremely high dimensional accuracy, ensuring that the dimensions of the sprocket chain meet the most demanding engineering requirements.
Surface smoothness:Grinding can produce a very smooth surface, reduce the friction of the sprocket chain during movement, and improve transmission efficiency.
CTS uses advanced CNC grinders and high-efficiency grinding tools to ensure that each component of the sprocket chain can achieve the expected dimensional accuracy and surface quality. The meticulous grinding process is an important step in ensuring high-quality sprocket chain manufacturing.
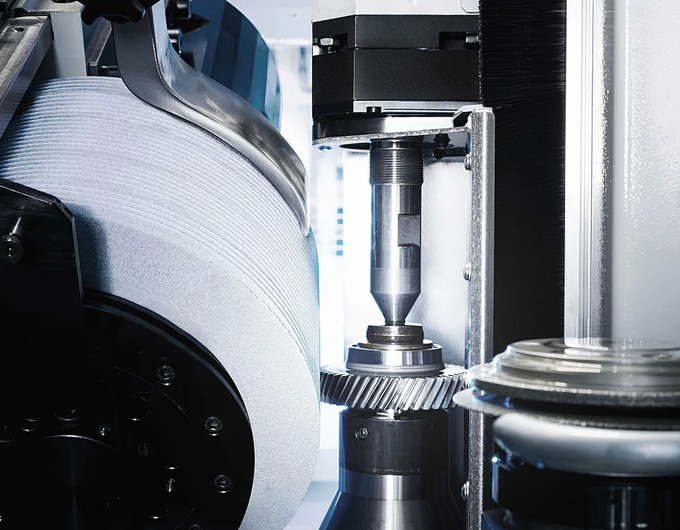
Application of technological innovation
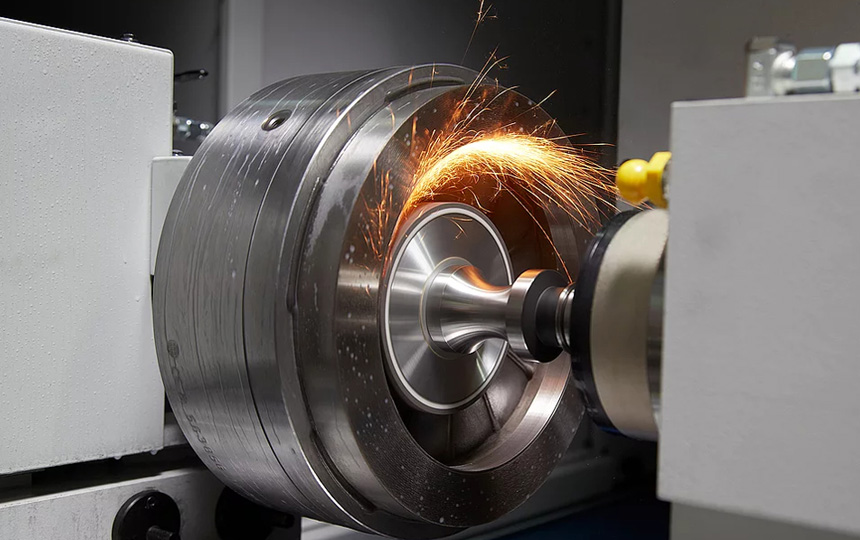
Get a quote online now and find out the cost of customization immediately.
Get a quoteCTS case
The sprocket chain customized for us by CTS performs extremely well in harsh agricultural environments. Meticulous control of the assembly process ensures products maintain excellent performance under high loads and corrosive environments. We no longer face frequent damage and repair problems, which greatly improves the reliability and service life of our agricultural machinery.
Thanks to CTS, the sprocket chain maintenance cost of our transportation vehicles has been reduced a lot. Every step is strictly controlled, from the quality of parts to the fit of the final product, which makes us deeply aware of their dedication to quality. We see it The product life is significantly extended, which directly affects our transportation efficiency and economic benefits.
After choosing CTS transmission equipment, the reliability of our equipment has been significantly improved. Zero error ensures the perfect fit of each component, reduces downtime, and truly injects strong power into our production efficiency. Their professional team and advanced technology make us confident in the quality of our products.
Make an appointment online now to visit the factory and experience our assembly process first-hand.
Our commitment to quality
Continuous improvement
We are not only satisfied with meeting current quality standards, but also committed to continuous improvement. We continuously improve our quality levels through customer feedback, internal reviews and technological innovation.
Transparent communication
We maintain transparent communication with our customers and provide detailed quality reports and performance data. We believe transparency is the foundation for building trust.
Quality Assurance
Our products undergo multiple inspections and tests to ensure they meet the highest quality standards. We have a strong guarantee on the quality of each sprocket chain.
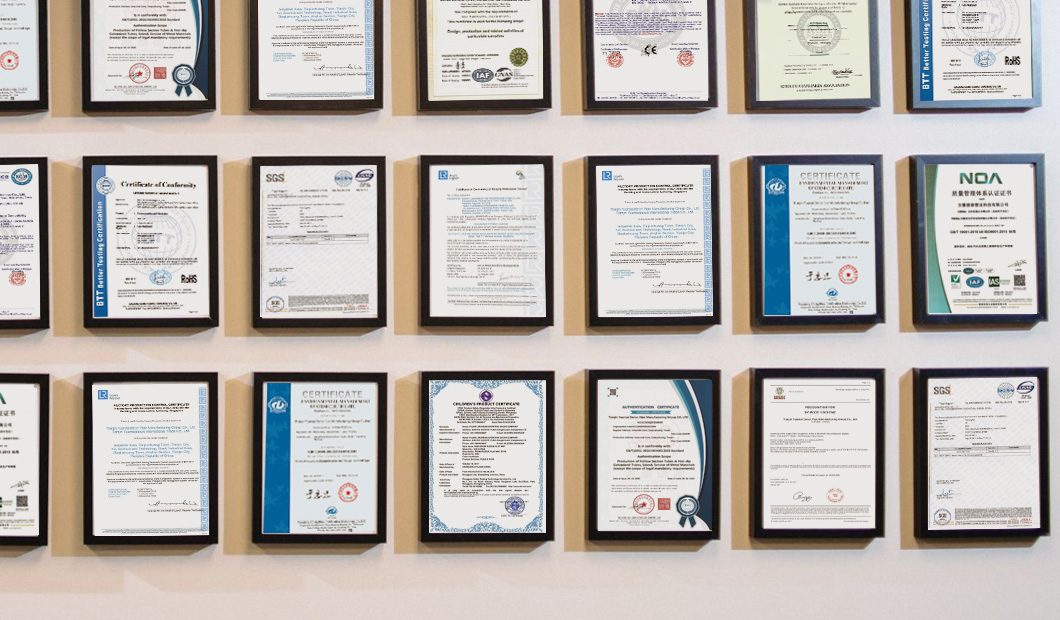
Technological innovation cases
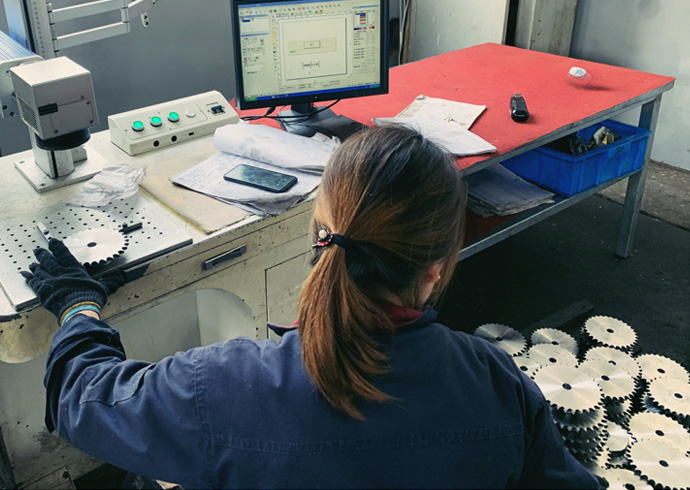
Case 1
CAD design and simulation optimization
We used CAD design and simulation technology to successfully optimize the gear structure of the sprocket chain. Through accurate mathematical models, we improved the shape of the gear, reduced friction loss, and improved transmission efficiency. Customers reported that the noise of the sprocket chain is significantly reduced and the performance is more stable when running at high speed.
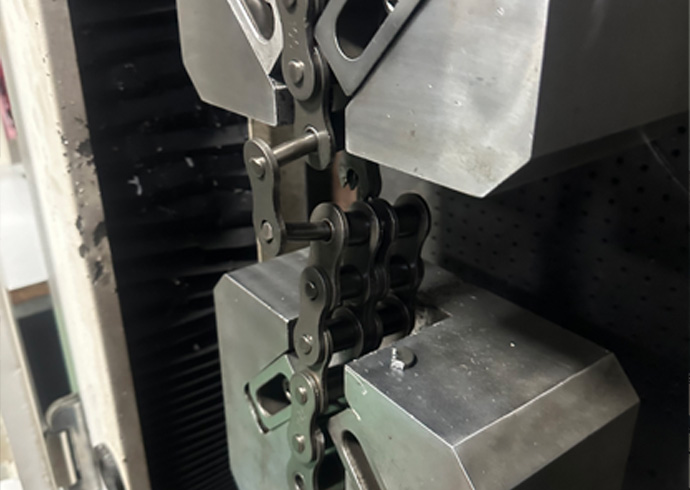
Case 2
Material technology upgrade
We used CAD design and simulation technology to successfully optimize the gear structure of the sprocket chain. Through accurate mathematical models, we improved the shape of the gear, reduced friction loss, and improved transmission efficiency. Customers reported that the noise of the sprocket chain is significantly reduced and the performance is more stable when running at high speed.
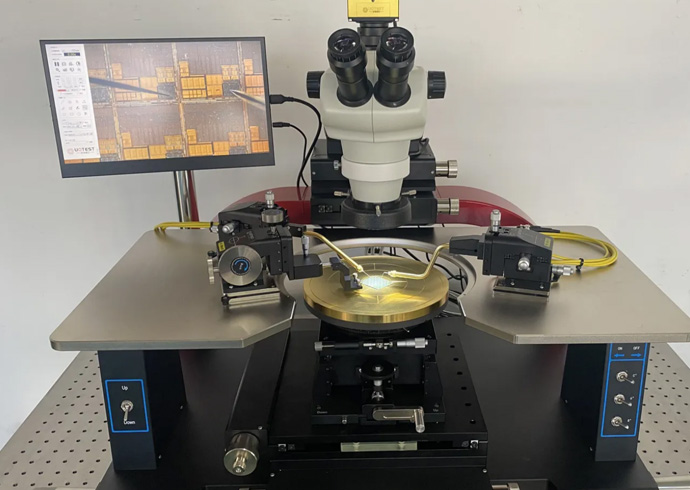
Case 3
Surface Treatment Technology Innovation
We used CAD design and simulation technology to successfully optimize the gear structure of the sprocket chain. Through accurate mathematical models, we improved the shape of the gear, reduced friction loss, and improved transmission efficiency. Customers reported that the noise of the sprocket chain is significantly reduced and the performance is more stable when running at high speed.
Ask The Experts
Having trouble finding the product you need? Send us an email with your question or message, and we'll quickly respond with tailored solutions. We're eager to hear from you! Expect top-notch precision, reliability, efficiency, and performance. Let's redefine excellence together.